Grid Couplings
Also called teeth couplings, these
couplings reduce vibration, and compensate for misalignment while transmitting torque. They offer the high torque capacity of a gear coupling and the flexibility of an elastomer coupling, providing a cost-effective solution.
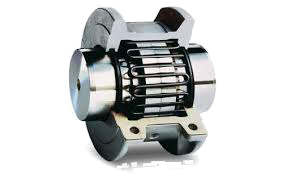
Grid couplings are a type of flexible coupling that can absorb shock, reduce vibration, and compensate for misalignment between two shafts. They have a spring-like grid that spreads out impact energy over time, which reduces the peak loads and protects the machinery. As the load increases, more of the tooth comes into contact with the grid, providing better protection and performance.
Grid Couplings are fully interchangeable between manufacturers. The grid coupling is noted for being simple to install and maintain, reducing downtime.
Contact Chain & Drives to assist in identifying the right grid coupling for your application.
Features & Benefits
- In the event of severe overload, grid breaks and prevents damage to high capital cost connected equipment.
- GS Grid Coupling comes with optional Horizontal Split case.
- When the parallel misalignment is too severe, the relating machine is protected by the virtue of shearing Grid or Tooth.
- Service life of connected equipment including bearings and seals are extended due to Grid Coupling smooth high torque capabilities.
- Quick installation and easy maintenance reduce labour cost and downtime costs.
- GS Grid coupling is interchangeable with international industry standard brands.
- 100% transmission of power at low noise emission.